Many of our customers ask the following question when they find out their backflow device has failed and will need to be repaired: “How much will it cost?” Unfortunately, there’s no easy answer to that question – at least without further examination.
Have you ever had a toothache? You know the feeling – your tooth starts to hurt and becomes sensitive to hot or cold temperatures, or both.
So, you head to the dentist and tell them you’re in pain. They explain that they’ll have to take some X-rays to find out what’s going on. Based on your symptoms, the dentist may infer that a cavity is causing the pain. However, in order to know the exact problem, and more importantly, how severe it is, they’ll have to take a closer look.
Once the X-rays are done, the dentist can tell whether you have a cavity, and they will know how bad it is. By examining inside the tooth, the dentist will determine that you do have a cavity, and they will identify the procedure required to remedy the situation. You may need a simple filling, or perhaps a root canal. In more extreme cases, the dentist may call for an extraction.
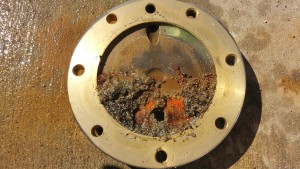
While an x-ray is a rather rough metaphor for a backflow test, it will help you visualize the situation. Your backflow service provider might inform you that your device has failed and will need to be repaired. While a test can determine which component stopped working, it is quite difficult to know the source of the problem without looking inside.
Here is an example: Say your backflow test results revealed a leaking #1 check valve. There are many reasons why this might have occurred, and in order to find the exact reason, you will need to look inside the device. Here are some of the frequently cited reasons for a leaking #1 check valve. (Remember the X-ray analogy.)
- Debris (such as grit or foreign material) is stuck in the check valve disc and allowing water to leak through. In this case, a simple cleaning might solve the problem.
- Debris is stuck between the check valve disc and the seat. In this case, it leaves an impression in the disc, so the rubber/silicone part will need to be replaced.
- The seat is cast into the body of the backflow and has worn out in several spots, causing a rough edge for the check valve disc to rest upon. This cannot be repaired, and the backflow device will have to be replaced.
Hopefully this will help you visualize the circumstances surrounding a failed backflow device more clearly. The examples above are only a few of the common symptoms of a failed backflow preventer. Note that there are many other possible reasons why your device failed the annual inspection.
If you would like to fix your backflow device yourself, please look here for important information and some great resources, including our favorite places to get parts.
And if you would like a second opinion, please feel free to contact us. You can schedule an appointment right away.
*Note: At Acute Backflow, customer satisfaction is our main concern. As we work toward continuous improvement, we’ll be providing reference pictures of all the conditions found during the evaluation of your backflow device(s).